Showing 15 results for Iron
Sheikh Abdolhossein A., Nili Ahmad Abadi M.,
Volume 1, Issue 3 (9-2004)
Abstract
In the present research influences of different combinations of five types of inoculants and four types of nodularizers on eutectic nucleation in ductile cast iron were studied. The alloys were kept at 1320°C for 0, 5, 10, 15 and 20 min under nitrogen atmosphere. Cooling curves and image analysis were used to characterize the influence of holding time and different combinations of inoculants and nodularizers on the graphite morphologies and eutectic nucleation. When dominant morphology of graphite is spheroidal or flake, by decreasing the different combinations of nodularizers and inoculants fading resistance, temperature of eutectic undercooling decreases. Nevertheless, when there is combination of spheroidal, vermicular and flake graphites temperature of eutectic undercooling increases by reduction of material fading resistance.
M. Adjabshiri, S. Sharafi,
Volume 4, Issue 1 (6-2007)
Abstract
Abstract: Strength at elevated temperatures and thermal shock resistance of austempered ductile
irons at high temperatures has been less intentioned, because of instability of ausferrite phase. In
this research the tensile properties of this iron and pearlitic ductile cast iron have been
investigated by short time high temperature tensile tests. Also thermal shock tests were done at
the molten lead bath at 1000 C . In these experiments, at first samples were immersed partially in
the molten lead bath for 25 seconds and then either cooled in air or quenched in water. Results of
short time high temperature tensile and thermal shock tests showed that ADI samples have higher
strength and shock resistance than the pearlitic ductile samples.
G. H. Akbari, M. A. Sheikhi,
Volume 4, Issue 1 (6-2007)
Abstract
Abstract: Ball mills are used in the last stage of ore processing for grinding raw materials. Forged
70Cr2 alloy steel and Austempered Ductile Iron (ADI) balls are materials from which grinding
balls are made for Sarcheshmeh Copper Plant (SCP) ball mills. In the present study wear and
impact properties of these two kinds of balls have been investigated. Some balls randomly were
selected as samples. They were cut to investigate the cross section under optical and scanning
electron microscopes. The microstructure of the sample balls was studied and quantitative
measurements of microstructural features were performed. The hardness of different parts of cross
sections of balls was measured. The wear resistance of the balls was measured by Pin on Disc
method. Repeated dropt test was employed to evaluate impact resistance of the balls. The
microstructure of ADI balls consisted of bianitic matrix with graphite nodules and some retained
austenite and martensite. Micro cracks and porosities in the cast structure were frequently
observed. In the case of forged steel balls the microstructure composed of tempered martensite in
outer area and bianitic structure with some tempered martensite in central areas. The wear and
impact resistance of forged steel balls were markedly higher than those of ADI balls. The
difference was consistent with the differences between the microstructures of the two kinds of balls.
Cast structure with microcracks and shrinkage porosities in ADI balls gives rise to lower impact
resistance.
M. Aazami, A. Khodadadi, A. Farzanegan,
Volume 4, Issue 3 (12-2007)
Abstract
Abstract: The specific rate of breakage is one of the most important factors in evaluation of
grinding process especially in ball mill. In this article the effect of ball size and feed size on
selection function were investigated using batch grinding circuit on two-iron ore anomaly (B, C)
from sangan mine in north of Iran. Eight different monosize fractions were prepared between 2000
and 500 microns, using a 2 sieve series. The specific rates of breakage (Si) were determined from
the size distributions at different grinding times, and the specific rates of breakage were compared
for three different ball diameters (25.4, 16.6 and 9.6 mm). The results showed that the breakage
function of both anomalies is normalizable (independent to the particle size) and it is independent
to the ball size. But the specific rate of breakage variate with feed size and ball size. Also optimum
size of balls for grinding of this feed obtained to be between 9.6-16.6mm.
H. Mohammadzade, Sh. Kheirandish, H. Saghafian,
Volume 6, Issue 2 (6-2009)
Abstract
Abstract:
transition and heat affected zones formed during surface remelting (in order to improve wear resistance) with TIG
process has been investigated. Relationship between various TIG parameters and thickness of remelted and heat
affected zones revealed that a high concentrated heat energy is imposed by TIG process which makes it a proper option
for focused surface treatment. Based on microstructural examinations five areas with different microstructure and
microhardness were identified within the surface area. Graphite flakes were totally dissolved within the first area
leading to the transformation of denderitic austenite to plate martensite and the formation of ledeburite within
interdenderites. The main feature of the second area, resulted from the presence of graphite flakes, was the local
melting with a gap in the vicinity of graphite flakes and that of third area was the formation of finer and denser
martensite plates closer to the graphite flakes compared with those formed at a further distance. In the fourth layer
there is a mixture of martensitic and pearlitic matrix while the matrix of fifth layer has no change of microstructure.
In this study the effect of graphite flakes present in a pearlitic grey cast iron on the microstructure of melted,
F. Kashaninia, H. Sarpoolaky, A. R. Bagheri, R. Naghizadeh, M. Zamanipour,
Volume 8, Issue 4 (12-2011)
Abstract
Abstract: There have been lots of studies to control the poor hydration resistance of dolomite refractories one of the
most effective solutions has been the addition of magnesia to doloma. Using a co-clinker of magnesia-doloma as a
starting material would provide more homogeneity in the properties of the product and has been published recently.
On the other hand, addition of iron oxide to doloma has been found to increase the hydration resistance. In this paper,
the effect of iron oxide addition on hydration phase analysis and microstructure of two different magnesia- doloma
samples, one with CaO content of 25 wt% and the other one with that of 35 wt% has been investigated. Ten samples
were prepared by pressing followed by firing at 1750 ºC for 3hrs. Results showed that the hydration resistance of the
samples improved by decreasing the CaO content, because CaO is much more prone to hydration comparing to MgO.
Besides, iron oxide addition lead to the formation of iron-containing phases which increased the hydration resistance
of the samples both by capsulating the CaO and MgO grains and by promoting the liquid phase sintering.
M. H. Hemmati, J. Vahdati Khaki, A. Zabett,
Volume 12, Issue 3 (9-2015)
Abstract
The volatile matter of non-coking coal was used for the reduction of hematite in argon atmosphere at nonisothermal condition. A thermal gravimeter furnace enable to use an 80 mm-height crucible was designed for the
experiments to measure the weight changes of about 10 grams samples. A two-layered array of coal and alumina and
four-layered array of iron oxide, alumina, coal and alumina was used for the devolatilization and reduction
experiments, respectively. The net effect of volatile reduction of Fe
2O3was determined and it was observe that 45%
reduction has been achieved. Three distinct regions were recognized on the reduction curve. The reduction of hematite
to magnetite could be completely distinguished from the two other regions on the reduction curve. At 600-950°C, the
reduction was accelerated. 63% of volatile matter resulted in 25% of total reduction before 600°C while the remaining
volatile matter contributed to 75% of the total reduction. From the reduction rate diagram, the stepwise reduction of
the iron oxides could be concluded. The partial overlap of the reduction steps were identified through the XRD studies.
The starting temperature of magnetite and wüstite reduction were determined at about 585°C and at 810°C,
respectively.
M. R. Khorram, M. R. Shishesaz, Iman Danaee, D. Zaarei,
Volume 13, Issue 1 (3-2016)
Abstract
The micro layers micaceous iron oxide and nano-TiO 2 were incorporated into the epoxy resin by mechanical mixing and sonication process. Optical micrographs showed that the number and diameter size of nanoparticle agglomerates were decreased by sonication. The structure and composition of the nanocomposite was determined using transmission electron microscopy which showed the presence of dispersed nano-TiO 2 in the polymer matrix. The anticorrosive properties of the synthesized nano-composites coating were investigated using salt spray, electrochemical impedance spectroscopy and polarization measurement. The EIS results showed that coating resistance increased by addition of micaceous iron oxide micro layers and nano-TiO 2 particles to the epoxy coatings. It was observed that higher corrosion protection of nanocomposite coatings obtained by the addition of 3 %wt micaceous iron oxide and 4%wt nano-TiO 2 into epoxy resin.
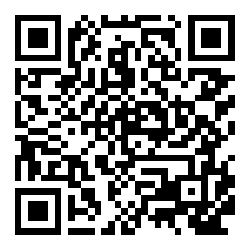
N. Alavifard, H. Shalchian, A. Rafsanjani-Abbasi, J. Vahdati Khaki, A. Babakhani,
Volume 13, Issue 3 (9-2016)
Abstract
In the present work, iron recovery from a low-grade hematite ore (containing less than 40% iron), which is not applicable in common methods of ironmaking, was studied. Non-coking coal was used as reducing agent. Reduction experiments were performed under various coal to hematite ratios and temperatures. Reduction degree was calculated using the gravimetric method. Reduced samples were subjected to magnetic separation followed by X-ray diffraction analysis. Total iron content, degree of metallization and recovery efficiency in magnetic part were determined by quantitative chemical analysis, which were obtained about 82%, 95% and 64% respectively under optimal conditions. CaO as an additive improved ore reducibility and separation efficiency. The microstructure of reduced samples and final products were analyzed by scanning electron microscopy. Final product with a high degree of metallization can be used in steel making furnaces and charging of blast furnaces which can improve production efficiency and decrease coke usage.
T. Mandal, D. Roy,
Volume 17, Issue 1 (3-2020)
Abstract
Magnetic iron oxide nanomaterials (MIONs) have been extensively investigated for the various important applications. Coprecipitation, hydrothermal, high temperature decomposition of organic precursors, microemulsions, polyol methods, electrochemical methods, aerosol method, sonolysis and green synthesis processes for the fabrication of MIONs have been reviewed. Different characterization methods like XRD, SEM, EDX and TEM for the as prepared MION materials have been studied. Important applications of MIONs in the field of biomedical, nanorobotics and energy devices have also been addressed in this review. Target oriented drug delivery and hyperthermia applications of MIONs have also focused
M. Monzavi, Sh. Raygan,
Volume 17, Issue 3 (9-2020)
Abstract
Low-grade iron ores contain many impurities and are difficult to upgrade to make appropriate concentrates for the blast furnace (BF) or direct reduction (DR) technologies. In this study, the beneficiation of an Oolitic-iron ore (containing 45.46wt% Fe2O3) with magnetization roasting by non-coking coal (containing 62.1wt% fixed carbon) under a stream of argon gas was investigated. Then, a 2500 Gaussian magnet was used for dry magnetic separation method. The effects of roasting time, ore particle size and reaction temperature on the amount of separated part and grade of the product were examined. It was found out that the hematite inside of ore could almost be completely converted into magnetite by stoichiometric ratio of coal to ore at the roasting temperature of 625 °C for 25 min. Under the optimum condition, a high amount of magnetic part of the product (72.22 wt%) with a grade of 92.7% was separated. The most important point in this process was prevention of reduced ore from re-oxidation reaction by controlling roasting atmosphere, time and temperature. In addition, different analytical methods such as X-ray fluorescence (XRF), X-ray diffraction (XRD), differential thermal analysis (DTA), thermogravimetric analysis (TG) and scanning electron microscopy (SEM) were applied to investigate and expound the results.
A. Kazazi, S. M. Montazeri, S. M. A. Boutorabi,
Volume 17, Issue 4 (12-2020)
Abstract
In the present study, austempering heat treatment was performed on compacted graphite aluminum cast iron with the chemical composition of 4.8%wt Al, 3.2%wt C, 0.81%wt Ni, 0.37%wt Mn, and 0.02%wt Mg. This study aims to investigate the effect of aluminum additions and removal of silicon on the kinetics of austempering transformation of Fe-3.2%C alloy. The cast samples were austenitized at 900 °C for 120 min and the isothermal austempering heat treatment was performed at 200 °C, 300 °C and 400 °C for 5, 30, 60, 120 and 180 minutes, respectively. Kinetics of this transformation was studied by X-Ray diffraction (XRD) analysis. The effect of temperature and time on the microstructure and hardness of the austempered samples was investigated and discussed. The presence of Al was seen to prolonged formation of the carbides from high carbon austenite, and that expanded the process window in the austempering transformation. Besides, the lower bainitic ferrite phase was observed in the austempered samples at 200 °C and 300 °C. Increasing austempering temperature to 400 °C changed the lower bainite to upper bainite structure. The volume fraction of austenite reached its maximum level (34.6 %) after austempering the samples at 400 °C for 30 minutes.
R.s Krishna, J. Mishra, A. Adeniji, Sh. Das, S. Mohammed Mustakim,
Volume 17, Issue 4 (12-2020)
Abstract
The field of nanomaterial has greatly advanced in the last decade following a wider range of applications in the fields of electronics, automobiles, construction, and healthcare due to its extraordinary and ever-evolving properties. Synthesis of the nanomaterial plays a crucial role in redefining the current engineering and science field. At the same time, procuring an environment-friendly end product through eco-friendly solutions and sustainable processes is the key to many global problems. Green synthesis of nanomaterials like graphene and its derivatives involves mild reaction conditions and nontoxic precursors because it is simple, cost-effective, relatively reproducible, and often results in more stable materials. This paper primarily focuses on the green synthesis of graphene and its derivatives (graphene oxide & reduced graphene oxide) and geopolymers; a green technology for preparing graphene reinforced geopolymer composites. Various methods used globally for green synthesis of graphene and geopolymer are briefly discussed and this paper tries to integrate these two areas for a green end product. Possible applications of these green composites are also discussed to provide insights on the current growth and developments.
Razieh Khoshhal, Seyed Vahid Alavi Nezhad Khalil Abad,
Volume 20, Issue 1 (3-2023)
Abstract
- In this article, the effect of graphite on iron-silicon interactions was investigated. It was found that, as graphite enters the iron structure, it permits further development of iron-silicon reactions. It was found that in the stoichiometric ratio of 1:0.5 of iron and silicon, when graphite is added to the system, simultaneously with the reaction of iron and silicon to form Fe3Si5, some amount of carbon can be dissolved in the iron and lead to more diffusion in iron and more iron silicide production. Silicon also reacts with carbon and produces SiC. The more amount of carbon entered into the system, the more growth of SiC occurs, while the production of other iron silicide phases, namely FeSi and Fe3Si preceded. Finally diffused carbon into the iron reaches a definite amount that can form Fe3C. In the stoichiometric ratio of 1:1 of iron and silicon, the formation of FeSi and SiC phases is observable. At the same time, the diffusion of carbon occurs in the same as the previous stoichiometric ratio. In the stoichiometric ratio of 1:2 of iron and silicon, compared with the stoichiometric ratio of 1:1, a larger amount of silicon is available and, the FeSi2 phase can form in addition to FeSi
Amruta Patil, Sonali Mahaparale,
Volume 21, Issue 1 (3-2024)
Abstract
Iron oxide nanoparticles has attracted extensively due to their supermagnetic properties, preferred in biomedicine because of their biocompatibility and potential nontoxicity to human beings. Synthesis of iron nanoparticles (FeNPs) was prepared with the help of ferric chloride and ferrous sulphate by using the coprecipitation method. The variation and combination of ferric and ferrous concentrations affect the physical and magnetic properties of iron oxide nanoparticles. The effect of 0.1 M ferric and ferrous concentration on iron oxide nanoparticles studied separately and in combination. The obtained nanoparticles were characterized by Particle size, zeta potential, Ultraviolet (UV-visible), Fourier Transform Infrared Spectroscopy (FTIR), X-ray diffraction (XRD), Scanning electron microscope (SEM), Thermal gravimetric analysis (TGA), and Vibrating-sample magnetometer (VSM) techniques. Particle size was below 200nm and zeta potential was within the limit for all the batches. UV visible spectra at 224 nm, and FTIR exhibit two peaks at 510 and 594 cm-1, indicating iron oxide NPs and XRD confirmed the crystalline nature of Fe. SEM showed a spherical shape for all batches. The use of a combination of ferric and ferrous is more effective than its individual use. TGA and VSM studies confirmed its magnetic properties.