Showing 9 results for Mechanical Alloying
Mrs Somaye Alamolhoda, Dr Saeed Heshmati-Manesh, Dr Abolghasem Ataie,
Volume 7, Issue 3 (8-2010)
Abstract
In this research an ultra-fine grained composite structure consisting of an intermetallic matrix together with dispersed nano-sized Al2O3 obtained via mechanical activation of TiO2 and Al in a high energy ball mill and sintering of consolidated samples. Phase composition and morphology of the milled and sintered samples were evaluated by XRD and SEM techniques Thermal behavior of the powder sample milled for 8 hours was evaluated by DTA technique. DTA results showed that, the reaction happens in two steps. The first step is the aluminothermic reduction of TiO2 with Al. XRD observations reveals that minor amount of Ti3Al phase formed during reduction reaction together with TiAl and Al2O3 major phases. This intermetallic phase disappeared when sintering temperature was increased to 850 ºC. The second step in DTA is related to a reaction between residual Al in the system (partly dissolved in TiAl lattice) and the Ti3Al phase produced earlier at lower temperatures. SEM micrographs reveal that by completion of the reduction reaction more homogeneous and finer microstructure is observable in sintered samples.
A. Karimbeigi, A. Zakeri, A. Sadighzadeh,
Volume 10, Issue 3 (9-2013)
Abstract
Ni and Cu elemental powder mixtures containing 25, 50, and 75% at Cu were subjected to mechanical alloying in a planetary ball mill under various milling times. Structural evolution was analyzed by means of X-ray diffraction and scanning electron microscopy. Experimental results indicated that nanostructured solid solution alloy powders having homogeneous distribution of Ni and Cu were formed by milling-induced interdiffusion of the elements. Average crystallite size of the as-milled powders was decreased with increasing Ni content and milling duration, and found to be in the order of 15-40 nm after 30 h of milling for all powder compositions. Moreover, lattice parameter and lattice strain of solid solutions were increased with the time of MA, which was more intense for nickel-rich alloys
M. Maddah, M. Rajabi, S. M. Rabiee,
Volume 12, Issue 4 (12-2015)
Abstract
In this study, the composite material with composition of MgH2-5 wt% SiC has been prepared by co-milling of MgH2 with SiC powder. The effect of milling time and additive on MgH2 structure, i.e. crystallite size, lattice strain, particle size and specific surface area, and also hydrogen desorption properties of obtained composite was evaluated by thermal analyzer method and compared with pure un-milled MgH2. The phase constituents and grain size of powder were characterized by X-ray diffractometry method. It has been shown that addition of 5 wt% SiC to MgH2 and mechanical alloying up to 30 h formed a nanocrystalline composite with the average crystallite size of 12 nm, average particle size of 0.5 µm and specific surface area of 10 m2/g. On the other hand, SiC can help to break up particles and reduce the particle size. As a consequence, the desorption temperature of composite material milled for 30 h has decreased from 435 °C to 361 °C.
Z. Sadeghian, R. Dezfulizadeh,
Volume 13, Issue 2 (6-2016)
Abstract
In situ Al2024- Mg2Si composite was fabricated by spark plasma sintering (SPS) of reactive powder. Reactive powder was obtained from mechanical alloying (MA) of elemental powders. Clad layers of in situ composite were fabricated on Al substrates by spark plasma sintering (SPS). Structural evolution during MA process and after SPS was investigated by X-ray diffractometery (XRD). Scanning electron microscopy (SEM) was utilized to study the microstructure of sintered samples. Hardness and tensile behavior of sintered samples were investigated. The results showed that SPS of mechanically alloyed unreacted powder can result in the in situ formation of Mg2Si and Mg2Al3 within the Al matrix. SPSed clad layer showed a sound and clear interface to the Al substrate with a hardness of about 140 HV. Sintered in situ composite exhibited a tensile strength of 288 MPa.
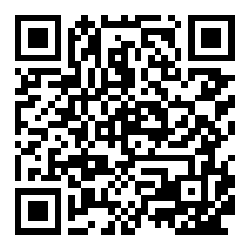
M. Paidpilli, K. Verma, R. Pandey, A. Upadhyaya,
Volume 14, Issue 1 (3-2017)
Abstract
In the present work, one batch of prealloyed 6061Al powder was processed by mixing and another one was ball milled with varying amount of lead content (0-15 vol. %). These powders were compacted at 300MPa and sintered at 590˚C under N2. The instrumented hardness and the young’s modulus of as-sintered 6061Al-Pb alloys were examined as a function of lead content and processing route. The wear test under dry sliding condition has been performed at varying loads (10-40 N) using pin-on-disc tribometer. The microstructure and worn surfaces have been investigated using SEM to evaluate the change in topographical features due to mechanical alloying and lead content. The mechanically alloyed materials showed improved wear characteristics as compared to as-mixed counterpart alloys. Delamination of 6061Al-Pb alloys decreases up to an optimum lead composition in both as-mixed and ball-milled 6061Al-Pb alloys. The results indicated minimum wear rate for as-mixed and ball-milled 6061Al alloy at 5 and 10 vol. % Pb, respectively.
Reza Mirahmadi Babaheydari, Seyed Oveis Mirabootalebi, Gholam Hosein Akbari Fakhrabadi,
Volume 18, Issue 1 (3-2021)
Abstract
Cu-based alloys have a wide range of applications in the electronics industry, communications industry, welding industries, etc. Regarding the type and percentage of the second phase, changing in the alloying elements has a significant effect on the mechanical and electrical properties of copper composites. The aim of the present work is to synthesize, investigate, and compare the micro-structure, micro-hardness, and electrical properties of different Cu-based nanocomposites. For this purpose, Cu-Al, Cu-Al2O3, Cu-Cr, and Cu-Ti were fabricated via ball milling of copper with 1, 3, and 6 weight percentages. The vial speed was 350 rpm and the ball-to-powder weight ratio was kept at 15:1. The milling process was performed at different times in Argon. Next, the prepared composites were studied by scanning electron microscopy (SEM), X-ray diffraction (XRD), and dynamic light scattering (DLS). Based on XRD patterns, crystallite size, lattice strain, and lattice constant were calculated by Rietveld refinement using Maud software. The results show a decrease of crystallite size, and an increase of the internal strain and lattice constant by rising the alloying elements in all composites. Then, the produced powders compressed via the cold press and annealed at 650˚C. Finally; the micro-hardness and the electrical resistance of the manufactured tablets were measured. The results of these analyses show that micro-hardness is increased by enhancement of the reinforcement material, due to the rising of the work hardening. Cu-6wt%Ti with 312 Vickers and Cu-1wt%Al2O3 with 78 Vickers had the highest and lowest micro-hardness, respectively. Moreover, the results of the electrical resistance indicate a dramatic rise in the electrical resistance by increasing the amount of alloying material, which Cu-1wt%Al with 0.26 Ω had the highest electrical conductivity.
Ehsan Tarighati, Majid Tavoosi, Ali Ghasemi, Gholam Reza Gordani,
Volume 19, Issue 1 (3-2022)
Abstract
In the present study, the effects of boron on the structural and magnetic properties of AlCrFeNiMnSiBx high entropy alloys (HEAs) were investigated. In this regards, different percentages of boron element were added to the based composition and the samples were identified using X-ray diffraction (XRD), scanning electron microscopy (SEM) and vibrating sample magnetometer (VSM) methods. Based on results, the tendency of Si element to formation of silicide phases prevents from the stabilization of single FCC and BCC solid solution phases in AlCrFeNiMnSi alloy. The boron element has significant effects on destabilization of silicide phases and by increasing in the percentage of this element, the simple BCC solid solution phase has been dominate phase. Of course, boron has distractive effects on magnetic properties of prepared alloys and the saturation of magnetization of AlCrFeNiMnSiBx HEAs decrease from 29.8 emu/g to about 6 emu/g by increasing the boron content.
Seyed Farzad Dehghaniyan, Shahriar Sharafi,
Volume 21, Issue 2 (6-2024)
Abstract
Mechanical alloying was employed to synthesize a nanostructured alloy with the chemical formula of (Fe80Ni20)1-xCrx (x= 0, 4). The microstructural and magnetic properties of the samples were investigated using scanning electron microscopy (SEM), X-ray diffraction (XRD), energy dispersive X-ray spectroscopy (EDS), and a vibrating sample magnetometer (VSM). Additionally, theoretical calculations were performed using density functional theory (DFT) under the generalized gradient approximation (GGA). Simulations have demonstrated that an appropriate quantity of chromium (Cr) can dissolve within the BCC-Fe (Ni) structure, resulting in a favorable enhancement of the magnetic moment of the lattice. The XRD results indicated that after 96 hours of milling, Fe (Ni) and Fe (Ni, Cr) with a body-centered cubic (BCC) structure were formed. With increasing milling time, the grain size decreased while the microstrain increased. The saturation magnetization (Ms) of Fe80Ni20 composition increased up to 32 hours of milling, but further milling (up to 96 h) resulted in a decrease in the saturation magnetization However, for the (Fe80Ni20)96Cr4 powders, milling up to 64 h caused a reduction in Ms. The coercivity (Hc) trend was different and increased with longer milling times (up to 96 h) for both compositions.
Majid Tavoosi,
Volume 21, Issue 3 (9-2024)
Abstract
The present study focuses on the phase and structural features of MnAl intermetallic compound during solid-state synthesis. In this regard, the milling process was done in differentMn50+xAl50-x (0<x<7.5)powder mixtures and the prepared samples were evaluated using X-ray diffractometer, scanning and transmission electron microscopy, differential thermal analysis and vibrating sample magnetometer. The results showed that the τ-MnAl magnetic phase with L10 structure could not be formed during the milling and low temperature annealing. During milling process, Al atoms dissolve in Mn network and a single β-Mn supersaturated solid solution (SSSS) form. The β-Mn (SSSS) phase is unstable and transforms into the icosahedral quasi-crystal as well as γ2-Al8Mn5 and β-Mn stable phases during subsequent annealing.